How the dew point affects scuba rebreathers
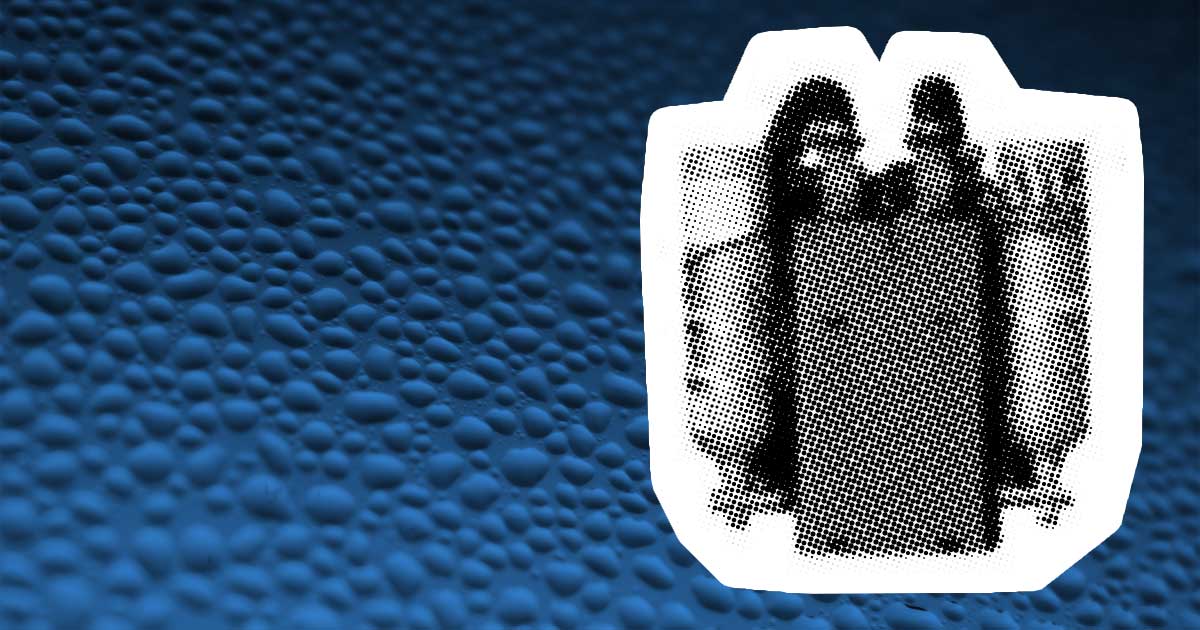
Why is humidity a key factor in rebreather systems?
As moist loop gas cools in a submerged rebreather, especially during descent. Condensation may accumulate on surfaces or within wiring and electronics, degrading system performance.
Humidity is a subject that few divers deal with continuously, and it is easy to misunderstand the various humidity scales. Dew point is a well-used and useful scale of humidity, independent of the temperature of a gas.
Trimix contains a mixture of gases, mainly helium, nitrogen, oxygen, and varying amounts of water vapour. The amount of a particular gas present may be expressed in terms of a partial pressure. The sum of the partial pressures exerted by each of the gas mixture components equals the total pressure. For Trimix:
Helium + Oxygen + Nitrogen + Water Vapour = Total Pressure
The wetter the air, the higher the partial pressure of water vapour will be.
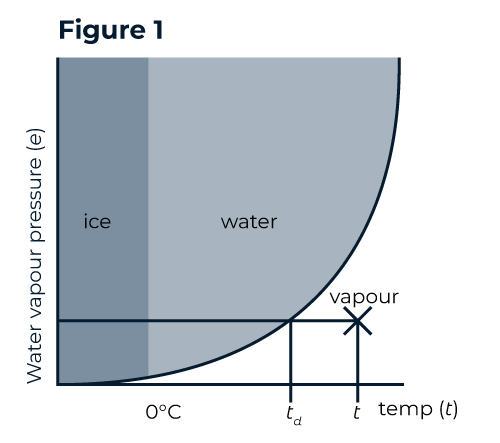
Warm gas can hold more water vapour than cool air. This can be likened to a sponge - the warmer the gas, the larger the sponge. Figure 1 illustrates the saturation curve of water vapour versus temperature. As temperature increases, more water can be held in the vapour phase.
Dew point (Td) is defined as the temperature to which the gas would need to be cooled for condensation to begin. If the gas is cooled further, more water will condense; the temperature and dew point are the same, and the gas remains saturated.
Therefore, it should be noted that water vapour has a partial pressure and makes up part of the breathing and the sensed gas. Rebreather control systems only measure the oxygen content of a gas for PO2 control; however, integrated controllers with decompression rarely make adjustments for vapour in the assumed inert gas fractions. Such inaccuracies can only be calculated if the gas content is known for that particular rebreather, as the oxygen sensors being positioned in different locations in a loop will vary vastly in supersaturation.
Such accuracy in gas content would only be beneficial where such data is critical; modern decompression devices have either built-in conservatism or user-adjustable conservatism that can be manipulated to take into account those unquantified variables.
The effect of pressure on the dew point
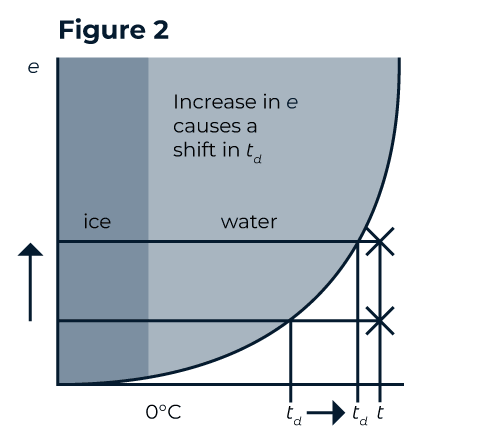
As a diver, it is important to know that the dew point also changes with pressure. With an increase in total pressure, each partial pressure is also increased: an increase in total pressure causes a shift in the dew point. This increase is like squeezing a sponge - gas is unable to hold as much water vapour under pressure. In Figure 2, the total pressure is doubled, and therefore, the vapour pressure due to water vapour is doubled. The result is that the dew point shifts. In rebreathers, where gas at atmospheric pressure is compressed to 7 bar or more, the vapour pressure rises a long way above the saturation curve, and condensation is observed.
To give you some perspective, if the loop gas you breathe is at 35°C on the surface, at 60m, the loop gas would have to be at 76°C to maintain the same dew point.
It is therefore important to accept that condensation will occur and there is little we can do about it. What we can try to do is prevent that condensation from causing problems with electronics and sensing systems.
Moisture and sub-systems
Condensation is not an immediate problem; it is a potential problem relating to the sub-systems. Pure distilled water conducts little electricity; it is the impurities in the water which give it the conductive properties. When we assume that there will be organic components as well as scrubber dust and other debris, we should assume some conductivity. If saline liquid were to make it into the loop, then we can be assured of it.
There are two main aspects of those systems we are concerned about:
- the electronics, including power supplies
- the oxygen cells
Moisture effects on rebreather electronics
From our earlier conclusions, it is pretty obvious that the water vapour is present anywhere there is gas from the loop. It is possible to mitigate the vapour by segregating the electronic components, coating them and using water-absorbent membranes or cartridges at the interface, but this has the disadvantage of being of limited life before it too is saturated and requiring post-dive maintenance.
The only other way is to separate the electronics from the loop entirely in its housing. Unless the electronics are in 1ATM housing, then there are equivalent levels of vapour in the electronics or battery housing, regardless of their physical construction.
Electronics on a rebreather system are varied and should be considered from the integrated controllers to the cables interconnecting subsystems. Most electronics circuits in such equipment are potted or encapsulated in a hydrophobic or displacing substance, such as a polyurethane two-pack. Alternatively, there is a substance that we call conformal coating that can work well.
Cables and their termination are a weak point in that they must, at some point, be exposed to the gas in question. This leads to some gas permeating inside the cable sheath and causing corrosion, or even worse, voltage leaks, which we describe as ‘Creepage’.
Protecting your wiring
Galvanic-assisted corrosion is of particular concern, given the fact that solder joints are comprised of different metals or alloys that are in contact with one another. Add to this a high oxygen content environment, and salts and any metals are at particular risk. To many, this phenomenon is countered by 'regular' maintenance, which usually means “replace when bad”. It is just as simple to design and construct using principles to avoid this corrosion in the first place.
Polyurethane two-pack compounds, which are not loaded with fillers, are relatively cheap and encapsulating joints is a simple and effective method. Let me explain, soldered joints in rebreathers can corrode by >0.15mm per year when inadequately protected. Oh, and heat shrink is not protection.
Inevitably, when cables and conductors are inadequately protected, the pressures exerted on the system promote migration of oxidising agents up the cable through the gaps between conductor strands. When considering the low voltages involved in closed-loop control systems in rebreathers, we can see how design criteria can be seen as a critical function of its design, not a secondary consideration of assembly. Marine cables are now commonly available that minimise or prevent this occurrence.
The importance of oxygen cells
Oxygen cells rely on a very small output voltage that operates between an effective 8-150mV output. Creepage acting on a system with such a sensitive instrument voltage range is significant.
If water vapour were to condense in the loop and form moisture, which it will, then that moisture would first collect on surfaces with a temperature lower than the gas. Eventually, almost all the surfaces will obtain some moisture and ignoring the effects of ‘wicking’, the liquid will attach to most surfaces. The level of conductivity of the liquid determines the level of detriment to the system.
An SMB or coaxial cell has a dielectric separation of about 5mm, which is fairly good. This is due to the labyrinth pattern of the engagement of the male and female parts of a plug/socket.
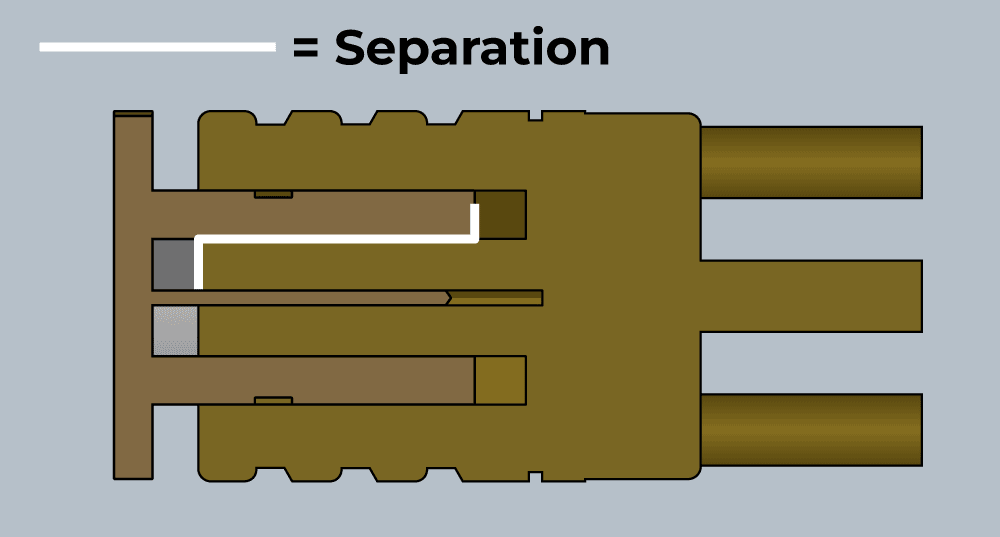
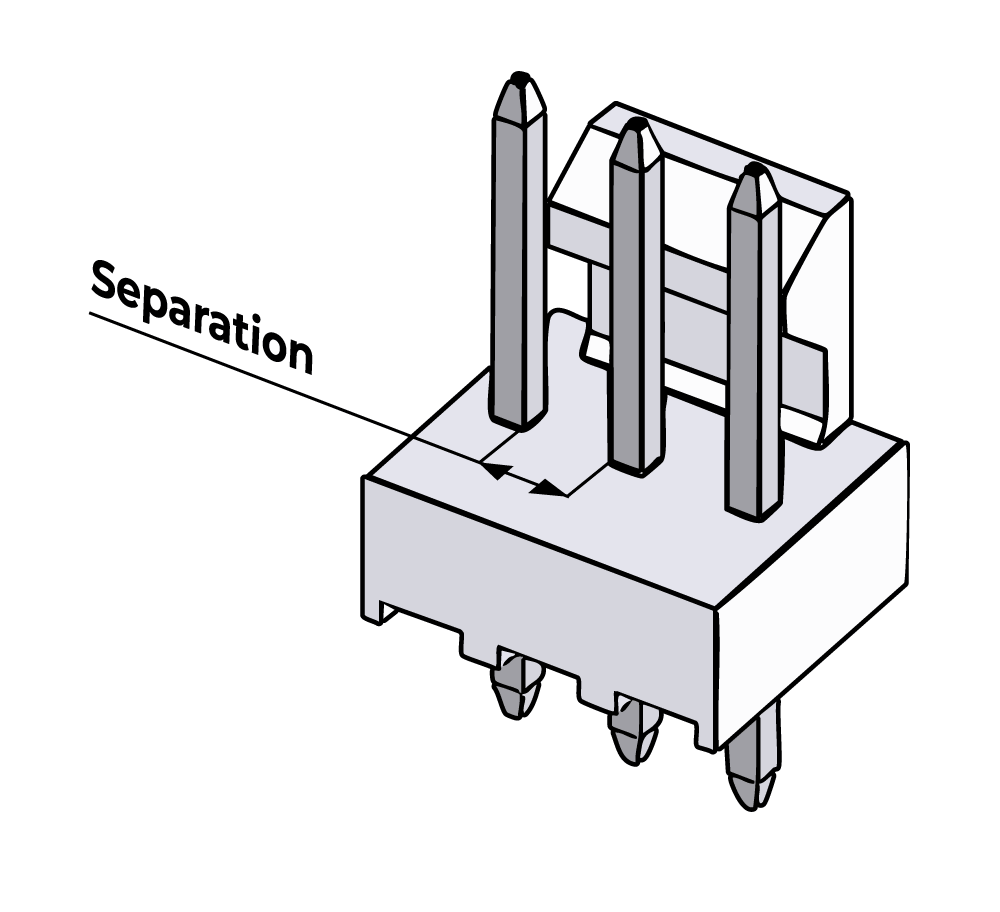
A Molex plug does not perform as well, and the separation is only the distance between the pins, which is a couple of millimetres.
An SMB cable socket still has a cavity where the conductor is soldered to the centre pin, and this should be potted with polyurethane to prevent any problems.
The cells themselves contain electronic components. This includes a resistor network and a thermistor or similar device to affect the temperature compensation. These components inside the cell should be encapsulated or coated in a conformal coating.
The important part of the cell concerning oxygen sensing is the face. Water condensing on the face of a sensor will have the effect of slowing down the response time of a sensor, and although humidity 0-99% relative humidity (non-condensing) has a minimal effect on the sensor, the water vapour in the humidified gas will appear as a lower than expected oxygen output.
So, conclude that in a rebreather, calibration of a cell with any occlusion on the face can lead to an incorrect correction factor being applied to the control system.
Remember this: the response time of a cell is a function of two parameters:
- The membrane. This is fixed at manufacture and stays constant throughout the sensor's life
- Henry's Law. The difference in pressure between outside and inside the sensor.
They are the facts governed by the physics of a sensor. However, external effects can alter what happens, such as water on the membrane and sensor age.
Near the end of the sensor's life, the anode surface is much smaller, so response time must increase (probably a very small effect until the last hours of the sensor). Measuring response time has no purpose as it is less enlightening than measuring a sensor's output at high PO2.